Kenneth Merchant on digital twins in the defence industry
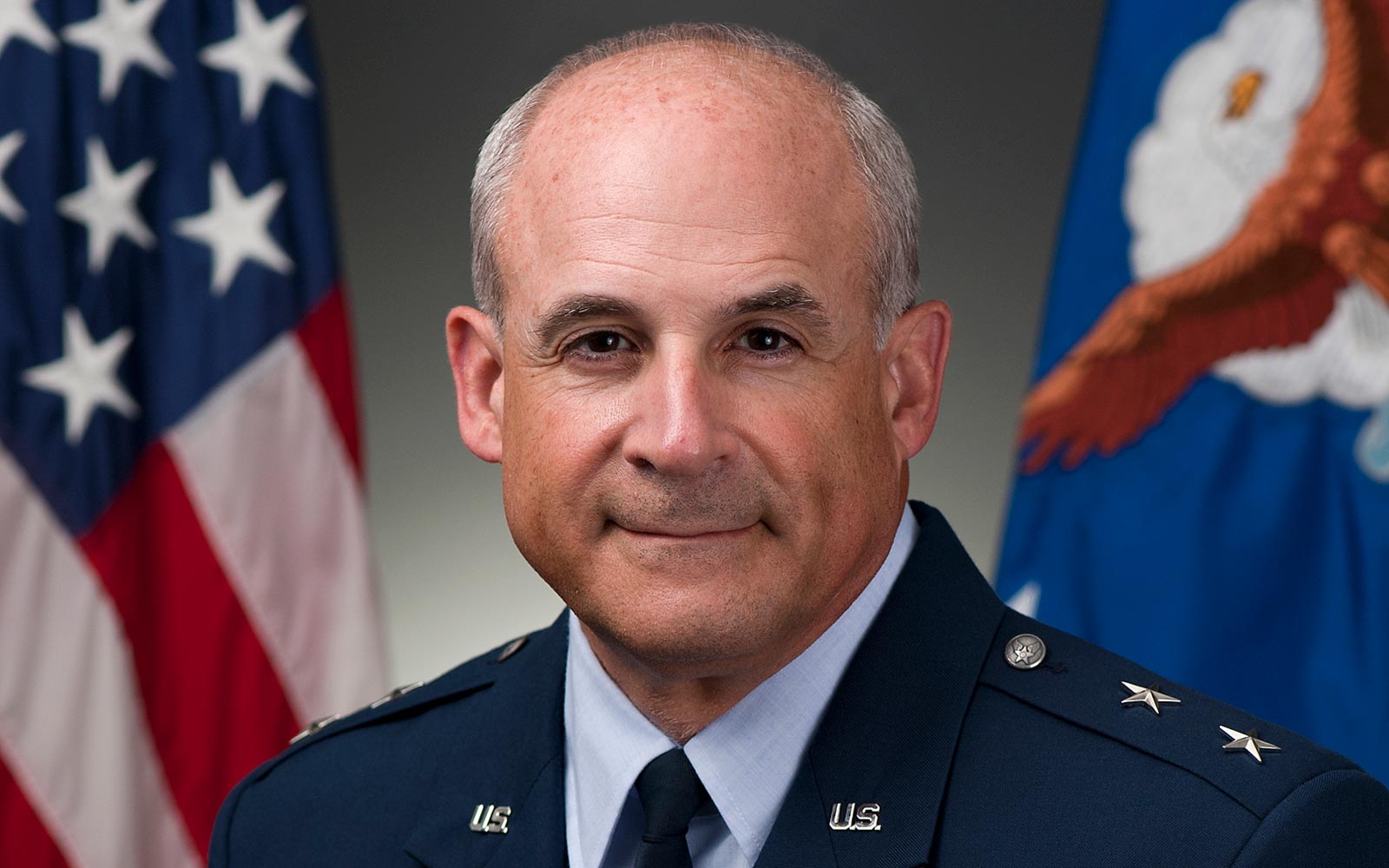
Ret. Major General Ken Merchant, special advisor to Aerogility
Ken Merchant has more than 40 years’ experience working in US defence, including a distinguished 34 years of service in the United States Air Force. Ken supports Aerogility as special advisor for US defence.
Previously, Ken was a vice-president on F-35 and F-22 programmes at Lockheed Martin Aeronautics. His vast experience includes the F-22 Raptor Enhancement, Development and Integration (REDI) programme. Major General Merchant served as a director in the US Air Force, with multiple experiences in global mobility programmes and logistics. His achievements include being awarded the US Air Force Distinguished Service Medal and two Legions of Merit, as well as the Bernard Schriever Award for Program Management Excellence for his work on the F-22 development programme.
Ken, what do you see as the main benefits of an enterprise digital twin in the context of the defence industry?
Digital twinning is a key design tool revolutionising the aerospace industry. It allows the design team to test out design theories well in advance of building a physical representation, which in turn saves considerable amounts of money, time, and human capital.
Can you share your experience in managing large defence programmes, and how digital twins could have enhanced the operation?
As you’d imagine, digital twinning saves a great deal of money and time over the processes we used when I first entered the industry nearly 45 years ago. One of my first experiences was managing the development of the LANTIRN Navigation Pod. Back then, we began by developing an initial design concept, built a breadboard and tested it in our labs. Once we showed signs of success, we’d iterate the design to the brass board stage, where it began to take more of a flyable look but was still a far cry from the final product. Finally, we’d produce the development unit, which underwent further lab testing and, ultimately, moved on to flight test.
This approach sometimes took years to produce the flyable test asset despite employing the most capable design tools available at the time. Sometimes, we’d get lucky and get close to right on the early iterations. Other times, we’d fail miserably and have to regroup after spending millions chasing ‘unobtanium’.
When I worked F-22 development in the mid-90s, we used CATIA to produce a digital version of what would previously be a collection of drawings. In the end, it was a digital representation of the product that allowed us to produce some pretty basic 3D models. I recall that during CDR (critical design review), we produced a fly-through video that took the viewer in one of the engine inlets and through the entire airframe. The modelling analysis at that time was pretty rudimentary by today’s standards, but advanced for its time.
Today, digital twinning not only compresses the overall design timeline, it provides the foundation for the production design and future modifications. As the design evolves into a version that can reliably be mass produced, new roles arise — modernisation and sustainment. These roles build off the original design baseline allowing a nearly unlimited number of what-if exercises to be run to achieve the desired effects. Need more range? Make it lighter and simulate 8000 flight hours on the new design. Need a part to stay on wing longer? Iterate and simulate.
How do you think digital twins enhance decision-making for military operations and logistics?
The military has done modelling and simulation for years. In fact, we ran models back in the days of breadboards and brass boards. The difference now is the incredible leap in computing power, and the introduction of artificial intelligence and machine learning. As the tools learn to think like we do, they can replicate our engineering and business practices in ways we could only imagine. These processes occur much faster than ever before, and they enable far greater detail to be introduced into the models.
I see new applications for digital twins and AI beyond the design and production activities. These tools can be used to better predict budget needs on a longer term. With these new and evolving tools, we can replicate the actions of a group of workers on a repair line, or break it down to each individual in the group. Once we teach the tool how the group interacts and what constraints they operate under, we can iterate the model to find greater efficiencies.
When I led Lockheed Martin’s F-22 program, we were mystified at the lack of production on one of our depot mod lines. An examination identified the main issue, which was a waning workforce. The F-35 had arrived, and many of our workers had moved to the new program. We were able to help our government supplier present the problem to its leadership and obtain special hiring authority to bring new employees online more quickly.
Had we employed digital twin and AI tools, we could have modelled the enterprise and projected the standard hiring and training processes to determine when the F-22 workforce would be recovered. We could also identify ways to accelerate the standard processes and bring them to bear to compress the timeline before we hired the first worker.
We could also insert and model line improvements such as new tooling and/or test equipment and identify the upfront investment, the lead time to acquire the tooling, test equipment, and any infrastructure needs to determine when those improvements and the added workforce will produce for the enterprise.
We can also insert real data as time goes on to identify any schedule impacts that will result from late hardware and components. These aren’t the traditional applications for the tools, but they show what’s in the art of the possible.
Can you share a specific project where you or Aerogility successfully implemented a digital twin? What was the outcome?
I know of one specific customer, Rolls Royce, who has adopted our tool set as their primary strategic planning and digital twinning tool across their entire defence segment. It enabled them to successfully project 100 years of overhauls before producing the first production engine. Digital twinning allowed them to modify materials and adjust other design factors to improve reliability and determine the right overhaul frequency.
Imagine being able to fly a design to full-life before building the first unit and then adjusting the design, or possibly modifying the requirement, to produce a lower ownership cost.
Check out other posts where you can meet the rest of the team or email us for more information on this story.